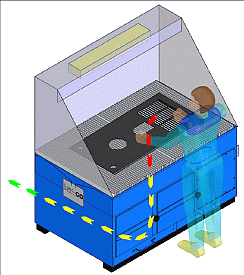
Down Draft Tables
Sometimes the best solution for extracting welding fumes is right on the table. This is generally referred to as a Down Draft Table. The Downdraft Table serves as both a workbench and an air cleaner. A rigid grill supports the product, while an air cleaner below draws smoke and fumes down and away from the worker's breathing zone. A worker can weld, grind, and cut on the surface of the table while dust and fumes get sucked away from breathing air space.
By combining the extraction system with a workbench, downdraft tables are very effective for safe work environments, and space-saving solutions. Soldering, spray-painting, and other benchwork applications are exactly what our downdraft tables are for.
- Aerospace - Aluminum Welding
- Aerospace - Deburring
- Aerospace - Painting and Marking
- Aerospace - Steel Welding
- Art's - Cleaning with Solvents and VOC's
- Art's - Jewelry Manufacturing
- Auto body repair - Aluminum Welding
- Auto body repair - Buffing and Polishing
- Auto body repair - Deburring
- Auto body repair - Painting and Marking
- Auto body repair - Steel Welding
- Chemicals and Plastics - Pesticide Manufacturing
- Chemicals and Plastics - Resin Manufacturing
- Chemicals and Plastics - Soap Manufacturing
- Construction - Paint Spray Gun
- Educational - Machine Shop
- Educational - Welding Shop
- Educational - Wood Shop
- Electronics - Electronics Assembly Line
- Farm & Heavy Equipment - Farm Equipment Repair
- Farm & Heavy Equipment - Heavy Equipment Repair
- Farm & Heavy Equipment - Steel Welding
- Forensics - Forensic Laboratories
- Machine Shop - Abrasive Cut-Off Saw
- Machine Shop - Aluminum Welding
- Machine Shop - Hand Grinding Bench
- Machine Shop - Metal Polishing Belt
- Machine Shop - Portable Chipping and Grinding Table
- Machine Shop - Steel Welding
- Marine - Aluminum Welding
- Metalworking - Aluminum Welding
- Metalworking - Steel Welding
- Mining & Quarrying - Drilling
- Misc. Operations - Mortuary Table
- MRO - Aluminum Welding
- MRO - Heavy Equipment Repair
- MRO - Painting and Marking
- MRO - Steel Welding
- Municipal & DOT Garage - Steel Welding
- Museums & Artifacts - Artifact Cleaning
- Museums & Artifacts - Paleontology
- National Defense - Aluminum Welding
- National Defense - Ammunition Manufacturing
- National Defense - Military Vehicle Repair
- National Defense - Steel Welding
- Painting - Small Paint Booth
- Paper & Leather - Paper Strengthening
- Public Transportation - Bus Maintenance and Repair
- Public Transportation - Subway Maintenance and Repair
- Vehicle Repair - Buffing and Polishing
- Welding Shops - Aluminum Welding
- Welding Shops - Copper Alloy Welding
- Welding Shops - Magnesium Welding
- Welding Shops - Nickel Welding
- Welding Shops - Stainless Welding
- Welding Shops - Steel Welding
Yes, but only when systems are configured, installed, and maintained for the correct use application. The filter selection is paramount to ensuring the reliability, effectiveness, and safety of the unit you use.
Downdraft tables are mainly designed with the idea of a workstation being integrated into the unit, so any application that requires fume extraction from a bench is ideal for a downdraft table. This includes soldering, grinding, spray painting, and welding. For a full list of industries, refer to our Industry Solution Page
To see a full list of products, check out our catalog below.
Some important points to consider when purchasing:
- Air Velocity: What is the velocity or the air required to pull the fumes and dust down into the table? (Add up the CFM for all of the inlets that will run at once)
- Face Velocity: What is the velocity at the Table surface required to achieve the appropriate capture velocity?
- Noise: Does your facility require a low operation noise level?
- Portability: Do you need the ability to reposition or maneuver the table?
- Orientation: Do you work standing up, or sitting down?
- Filter Cleaning: Does the filter cleaning system really work in your application?
- Surface Area: How much space to you need for your application?
- Capture Velocity: Can the filters accommodate the required capture velocity to capture the aerosol?
- Can the filters withstand the Pressure/abrasion/corrosion/etc.?
- Do I have enough filter media (air to cloth ratio) in the collector?
- Will it stand up to the working environment?
- e.g. is it made from plastic or steel?
- What will be my filter, maintenance, and energy costs per year?
- Are there any tertiary risks such as fire, explosion, etc., that I need to consider?
Pro's:
- Portable options available
- Commercial options available
- Multi-purpose - doubles as a standard work-bench
- All steel construction
- Easy filter access - reduces maintenance time
- Multiple filter options
Con's
- Extraction is restricted to the bench surface
- Portability of the unit determines the range of extraction
Industrial workers are exposed to a variety of health hazards every day. As a result, these workers risk the possibility of becoming sick, ill, and in some cases, permanently disabled. According to a WHO estimate (WHO, 2000), unintentional poisonings led to 300,000 deaths in the year 2000.
It's our mission to diminish that figure, but it only works if the correct equipment is used, and configured correctly. Our team works to make the logistics of those questions as straightforward and coherent as possible, and as such, will work with you to provide you with the best extraction system that fits your worker's needs. This includes everything from accessibility and usability to longevity and reliability.
You can read more about the risks and preventions of fume extraction below:
OSHA
WHO
Dilution ventilation is designed with more of a commercial aspect in mind. As oppose to local exhaust ventilation, how dilution ventilation extracts contaminants is by diluting them with fresh air, which requires the contaminants to be airborne before being removed from the building. This means that all airborne contaminants ultimately spread throughout the building until being pushed through the ventilation exhaust system.
On the other hand, local exhaust ventilation captures contaminants at or near the source of the process. This eliminates the possibility of the contaminant becoming airborne in the first place. Eliminating the risk of airborne contaminant means that a buildings HVAC system does not have to filter industrial contaminants, which dilution ventilation is not designed to do. Some industrial contaminants are highly abrasive and corrosive. Rather than investing in the maintenance costs of the building multiple times, invest in the engineering control solution designed to deal with it.
To read up more about the benefits of local exhaust ventilation versus dilution ventilation, refer to these links:
CCOHS
Use of Local Exhaust and Dilution Ventilation
Our downdraft tables are all built using only mild and stainless steel, and finished in a very durable polyurethane powder coating, powered by a direct drive electric motor. We follow these requirements to ensure long life and minimal maintenance costs.
Filters:
We offer a selection of several filters, each designed for different workloads. Depending on contaminant, hours of use, and hazards associated with any given contaminant, we have a filter that will work for your needs. This way you don't need to worry about filters clogging prematurely, which avoids premature failure.
Motors: We use a direct drive motor on all of our extraction systems. Without the use of belts or pulleys in the driveline of the motor, associated maintenance costs are substantially lower, and allow you to get the most use out of your system without service intervals.